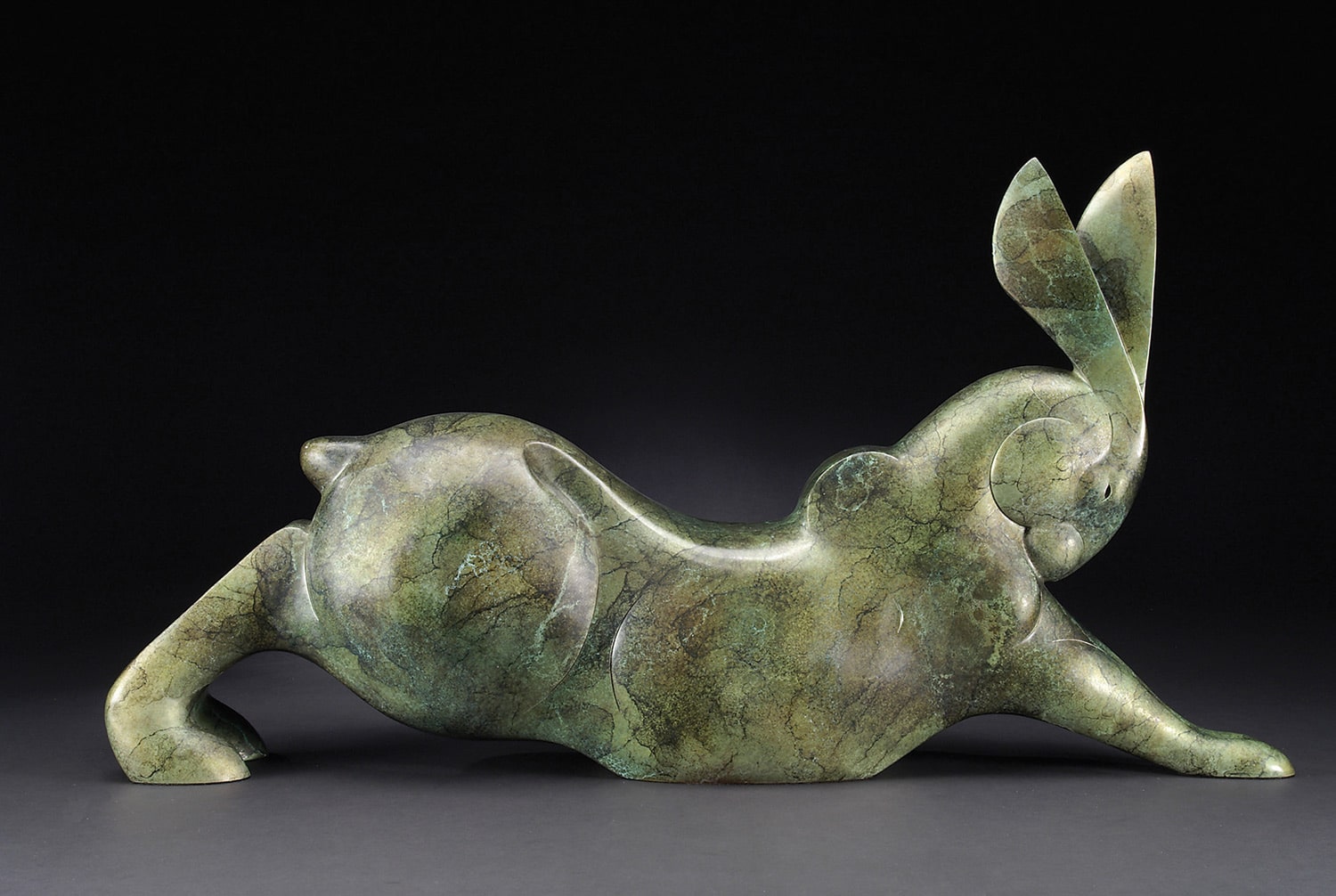
14 Sep Collector’s Notebook: Behind the Scenes at The Foundry
When a sculpture is cast at the foundry, the bronze comes out a nondescript, pale yellow. The rich, burnt umber look of burnished leather we associate with famous Western bronzes, such as those by Remington or Russell, comes from patination. And while most Western-themed bronze sculptures do use a traditional brown patina, a whole range of colors are possible, including blues and reds.
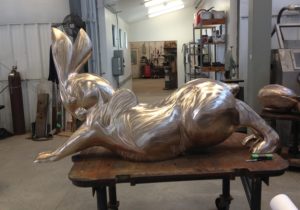
“Rabbit Reach” before undergoing the patina process. | All patinas: Patrick Kipper | All photos: Mel Schockner
Those who generate the distinctive patina on a finished bronze sculpture are rightfully called patineurs, or “patina artists,” and most sculptors acknowledge that the proper application of the patina is critical to the final aesthetic.
Missouri sculptor Tim Cherry explains that patination is an art process all its own, in part because the creation of those compelling finishing touches requires a good eye for color, a thorough knowledge of the chemical properties and actions of the various patination compounds, and skillful dexterity in the application of heat at the perfect temperature. The idea is simple: You have to heat the bronze to the right temperature (around 400 degrees in the case of Cherry’s work), and then spray or brush on various chemicals that oxidize the metal. “It sounds like the simplest thing in the world,” admits Cherry. “You’re just fooling with and controlling oxidation. But in practice, it requires a real feel for heat and the strength of the chemicals. And when the patineur does it right, the work comes alive. It’s amazing to see — really magical.”
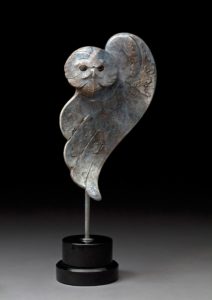
Tim Cherry, “Arctic Ghost” | Bronze | 19 x 8 x 5 inches
Like a lot of well-known artists, when it comes time for the patination of a sculpture, Cherry calls on one of the best-known patineurs in the world — Patrick Kipper. “For 30 years, I’ve had Pat Kipper do the patina on my pieces. He’s the leading expert on restoration work, the most knowledgeable of all the techniques, and the go-to man for modern work,” says Cherry. Most of Cherry’s sculptures involve smooth surfaces, which means the patineur “can play more and get some excellent marbling patterns. That approach wouldn’t work on a lot of Western art pieces that are more traditional and have more textured surfaces,” he says.
Having spent 43 years in the trade, Kipper is not only a master patineur but also an expert in conservation and restoration, as well as a teacher who travels the world, sharing his expertise. “You can’t underestimate the necessity of experience when it comes to patina,” Kipper states emphatically, pointing out that becoming a bona fide patineur requires seven years of study at minimum. This is true, even though Kipper can nutshell the basic principle of patination in one simple sentence: “Different chemicals at different temperatures yield different patination.” If that sounds a little too much like a scientific formula, Kipper can also describe the process in artistic terms: “You’re basically painting with heat and chemistry.”
Tim Cherry, “River Mates” | Bronze | 52 x 48 x 12 inches
Since both science and art merge in patination, it’s easy to understand how mastering the complex interaction among all the variables takes years of effort and experience. Consider the difficulty of getting the two most basic aspects of patination right: properly mixing the chemicals involved and applying the proper amount of heat.
Patina itself consists of a thin layer of oxidation that must properly adhere to the bronze if it is to look good and last. “That chemical film is from 5 to 20 microns thick,” Kipper explains. “Or about half the thickness of a human hair.”
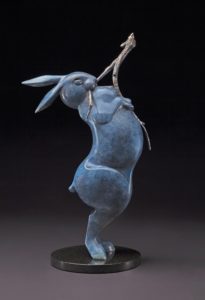
Tim Cherry, “Willow Snipper,” Bronze, 24 x 13 x 9 inches
Yet, that thin chemical veneer becomes a medium for a wide range of effects: depending on the reflective quality of the patina, the surface of the sculpture can take on depth and dimensionality, and the skillful patineur can produce a broad palette of colors. “When a sculptor comes to me unsure what they want the finished bronze to look like,” Kipper says, “I show them a board of sample squares of bronze with different colored patinas to choose from.”
Kipper has written two classic books in the field, Patinas for Silicon Bronze (1995) and The Care of Bronze Sculpture: Recommended Maintenance Programs (2007). While most of the artists he works with are master sculptors and know exactly what they’re looking for, Kipper’s expertise lies in coupling the right patina formulas to each piece. Certain compounds won’t work on smoothly finished bronze, for example, and some effects can overpower the already interesting features of a textured surface. And sculptures destined for the outdoors require a different patina from those that will be displayed on a desktop or a bookshelf. “An outdoor patina will be hardier, and then the piece will be lacquered and waxed,” Kipper says. Like everything else, patinas change over time, and outdoor sculptures ought to be washed and waxed a few times a year to maintain their integrity.
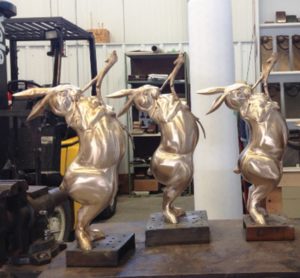
“Willow Snipper” before undergoing the patina process.
The celebrated Western sculptor and artist Edward Fraughton was among the first artists in the Intermountain West to do his own foundry and patina work, using techniques he characterizes as “non-standard and unconventional.” But, as with Kipper, he points out that the underlying principles are easily grasped, even if the mastery of putting them into practice takes years of experience. “Bronze responds differently to different chemicals and combinations thereof,” Fraughton says, “and to heat, moisture, cooling effects, etcetera.” Fraughton concurs that chemical formulas and the techniques with which they are applied matter a great deal in the finished sculpture. And, he says, the patina “can be transparent, opaque, or a combination of both to create a variety of aesthetic effects.”
Fraughton recommends Malvina Hoffman’s 1939 classic text Sculpture Inside and Out for anyone wanting to gain “a grasp on the old patination techniques.”
“In my mind,” Fraughton says, “the best patinas should be subtle enough to accentuate or serve the sculptural form and the material from which the final cast is made.”
Kipper expresses a similar view, stating his personal stake in the craft: “Patinas are designed to enhance the artwork, to bring the idea in the artwork forward. I’ve been doing this work for over 40 years, because I enjoy making a piece of metal look beautiful. And I feel honored to have the trust of so many artists.”
No Comments